Hablamos con Julia Contreras Fortes - Técnico de I+D -ACERINOX, SA, para detallar las claves principales para entender el desarrollo de la compañía en materia de sostenibilidad y los beneficios extraídos del programa FEDER INNTERCONECTA a través de los fondos europeos.
La compañía inició su actividad con el objetivo de poder suministrar acero inoxidable en formato plano a la industria nacional transformadora de chapa. Aunque esta última surge en 1960, la totalidad del acero se importaba desde Asia y Europa, principalmente desde Japón y Bélgica.
A causa de las expectativas de crecimiento para la siguiente década, tanto del mercado nacional como del internacional, se puso en marcha el proyecto de fábrica integral para la producción de productos planos de acero inoxidable.
De la respuesta a una necesidad al triunfo internacional
Su estratégico emplazamiento en la Bahía de Algeciras permitía la construcción de unas instalaciones portuarias que facilitasen las comunicaciones internacionales con los mercados de materias primas y productos acabados de acero inoxidable.
Un hito de su historia es el 30 de septiembre de 1970, cuando se constituyó en Madrid la Sociedad de Acerinox S.A., siendo el 65% de capital social del grupo español Banesto, Bandesco y Banco Guipuzcoano y el 35% restante del grupo japonés Nisshin Steel Co. Ltd. y Nissho Iwai Co. Ltd.
Varias fases de desarrollo y avance en los sistemas de producción, que comienzan en 1973, llegan hasta 1988, año en que se inauguró el Centro de Investigación y Ensayos de Acerinox. Otras de las líneas que ha sido fundamental para el éxito de Acerinox ha sido su red comercial, de modo que desde 1972 se distribuye material a nivel nacional y desde 1973 a otros mercados internacionales.
Tras la reciente adquisición de la compañía alemana VDM, fabricante de aleaciones de alto rendimiento, el grupo cuenta con 13 fábricas en 4 continentes diferentes, la compañía está presente en un total de 57 países a través de la red comercializadora constituida por 35 oficinas comerciales, 15 agentes comerciales, 18 centros de servicios y 25 almacenes. Además, cuenta con una plantilla total de 8.494 empleados, siendo el nivel de producción mundial en las acerías de 2.303.051 t; mientras que los productos del Grupo ACERINOX se pueden encontrar en 96 países en los 5 continentes.
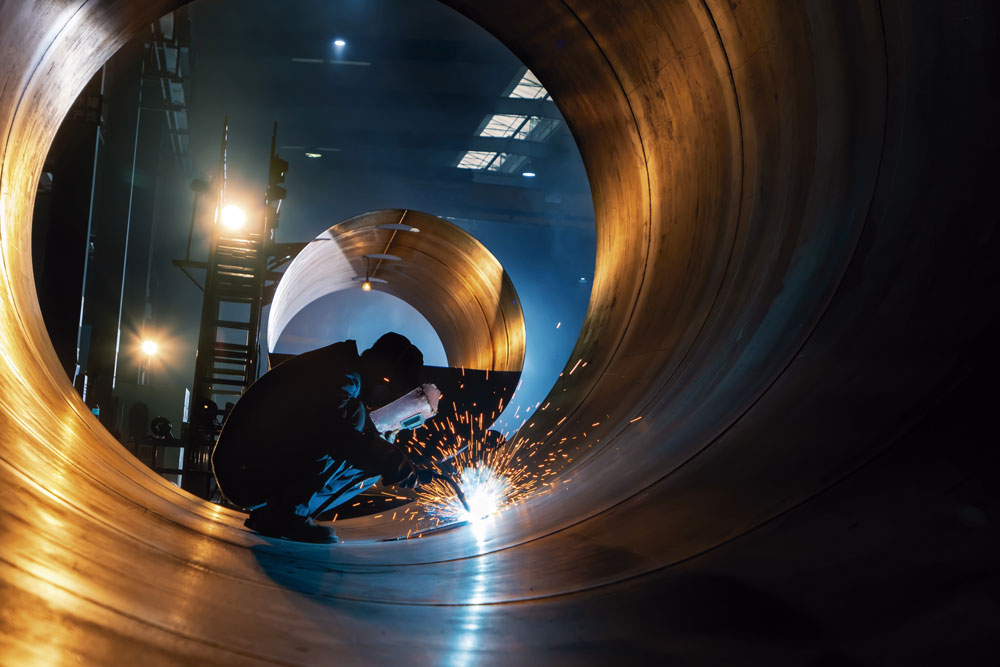
Las nuevas medidas suponen el ahorro de material, aligeramiento del peso, menor coste de fabricación y menor impacto medioambiental.
Más sostenible, más competitiva
A través del Programa FEDER INNTERCONECTA, Acerinox S.A desarrolló entre octubre de 2016 y marzo de 2019, un proyecto I+D cuyo objetivo era mejorar la eficiencia del uso de los recursos materiales y energéticos requeridos en la compleja producción de los aceros inoxidables dúplex, reduciendo su coste de fabricación y el impacto medioambiental de este material.
Esta necesidad venía motivada porque la compañía -que ha desarrollado su propia tecnología de fabricación para los aceros inoxidables dúplex de más consumo en el mercado (EN-1.4462 y EN-1.4362)- recientemente había puesto en marcha la producción de un tipo de acero dúplex de baja aleación (EN-1.4482) para competir con otros equivalentes ofrecidos por la competencia.
El desarrollo de estos aceros dúplex se había llevado a cabo de forma progresiva: primero los formatos menos exigentes de chapa gruesa con espesores comprendidos entre 10 y 50 mm; posteriormente bobina laminada en caliente con espesores entre 3.5 y 8.0 mm y por último bobina laminada en frío hasta 1.0 mm.
Julia expone que el problema surgió a raíz de la necesidad de un proceso especial para producir aceros inoxidables dúplex en producto plano con espesor final inferior a 1.0 mm, que consiste en una doble laminación en frío con una etapa intermedia de recocido, a diferencia del proceso requerido para la tradicional familia de aceros austeníticos. Este hecho suponía una penalización en términos de coste y de eficiencia energética de su proceso de fabricación.
Así, gracias a los recursos procedentes de los fondos europeos, por el programa FEDER INNTERCONECTA, se ha perseguido el objetivo de realizar modificaciones de composición química y de proceso que permitan fabricar diferentes tipos de aceros inoxidables dúplex, EN-1.4462 (2205), EN-1.4482 (2001) y EN-1.4362 (2304), en formato plano con un espesor final de hasta 0.5 mm mediante un proceso de fabricación estándar, en concreto con un único proceso de laminación en frío.
De este modo, Julia Contreras explica que la compañía ha logrado la producción de los aceros dúplex EN-1.4462, EN-1.4482 y EN-1.4362 en espesores menores de 1.0 mm a un coste más competitivo, mejorando su posición frente a sus competidores, tanto a nivel nacional como internacional, gracias a un producto de alto valor añadido. Este ha supuesto una ampliación de la gama de productos de estos aceros y también ha incrementado el campo de aplicación de los dúplex más allá de su nicho de mercado natural como es el sector estructural, hacia aplicaciones donde se precise un cierto grado de conformado (tipo tubos de pequeño diámetro, membranas, o recubrimientos) para sectores donde se requieran altas exigencias mecánicas y de resistencia a la corrosión.
Los principales beneficios que ha aportado el desarrollo obtenido por Acerinox para los clientes es el ahorro de material, así como un aligeramiento del peso, un menor coste de fabricación y un menor impacto medioambiental debido a la reducción de gases de efecto invernadero.
Actualmente, como detalla Julia Contreras, las conclusiones de este proyecto se están aplicando en los productos que fabrican.
Comprometidos con la sostenibilidad
El desarrollo de este proyecto, en definitiva, ofrece a la industria un producto de acero inoxidable con propiedades mejoradas, que lo convierten por tanto en un producto más sostenible; impacta menos en el medio durante su fabricación, y al mejorar sus propiedades y, en particular, mejorar su resistencia a la corrosión, se convierte en más duradero y así alarga su vida útil.
Cabe resaltar que el acero inoxidable, en ACERINOX, se fabrica con más de un 70% de chatarra de acero que alcanzó el fin de su vida útil, y que una vez alcanzado este fin de vida útil es 100% reciclable.
Con vistas al futuro, Acerinox ha presentado un Plan Estratégico hasta 2030 y cuenta con objetivos de sostenibilidad en todas las áreas. Así, existen cinco pilares fundamentales dentro del Plan que son:
- Gobierno ético, responsable y transparente,
- Ecoeficiencia y lucha contra el cambio climático,
- Economía circular y producto sostenible,
- Equipo comprometido, cultura, diversidad y seguridad,
- Cadena de suministro e impacto en la comunidad.
Se han elegido, además, seis indicadores claves en el ámbito ambiental y social, y se establecen unos objetivos corporativos; para la Huella de carbono (Alcance 1+2) se establece una reducción del 20%; para la eficiencia energética un 7,5%; para el agua, un 20% de reducción de captación; para residuos un 90% de valorización sobre lo generado; para el indicador de seguridad LTIFR (Lost Time Injury Frequency Rate), un 10% de disminución anual y finalmente para las minorías un aumento del 10% anual.
Acerinox S.A. apuesta, pues, firmemente por un futuro sostenible, una garantía de eficiencia y calidad para la provincia de Cádiz, que progresivamente se ve reflejada en cada una de las acciones de la compañía, de referencia nacional e internacional.